Soft Actuators and Sensors
We are developing various approaches based on porous hydrogels to optimize the actuation of flexible devices such as artificial muscles. We are also designing flexible nanomaterial-based sensors and intracranial pressure transducers.
Flexible Strain Sensors Based on Nanomaterials for Enhanced Stability
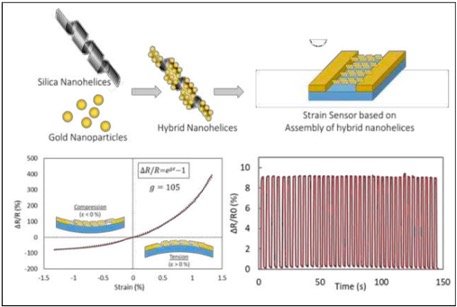
Flexible strain sensors based on nanoparticles (NP) find promising applications in innovative domains such as flexible touchscreens, connected health devices, electronic skin, and advanced robotics. Despite their potential, these sensors are traditionally limited by mechanical instability and pronounced hysteresis that compromise performance. To overcome these technological challenges, we propose an innovative solution: sophisticated sensors based on silica nanohelices (NH) functionalized with gold nanoparticles (AuNPs).
The developed strategy relies on a precise chemical approach. Gold nanoparticles, functionalized with mercaptopropionic acid and stabilized by carefully selected polymer ratios, enable optimization of colloidal stability and fine control of the insulating thickness. Through an innovative chemical coupling on the nanohelices, these AuNPs spontaneously organize into a unique helical arrangement. Their alignment between interdigitated electrodes, achieved by dielectrophoresis, confers remarkable properties to the sensor: increased flexibility, enhanced mechanical stability, and optimized sensitivity.
The experimental results are auspicious: these sensors demonstrate exceptional robustness, withstanding 2 million deformation cycles while maintaining constant sensitivity, thanks to the innovative structural architecture of the silica nanohelices.
Researchers
Vincent Mansard, Christian Bergaud
Engineers
Adrian Laborde, Fabrice Mathieu
Projects
- ANR Nanoheliflex 2015-2019 with IECB and ICMCB at Bordeaux, and the start-up Nanomade at Toulouse
- Maturation Project SATT Aquitaine 2022-2023
Publications
Highly stable low-strain flexible sensors based on gold nanoparticles/silica nanohelices, A. Amestoy et al., ACS Applied Materials and Interfaces, 2023, 15, 33, 39480–39493
Development of III-N MEMS on Flexible Substrates
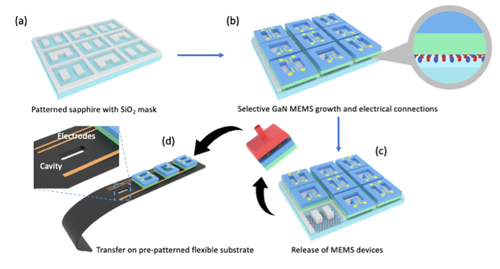
This project aims to explore the potential of a 2D material transfer technique for manufacturing III-N MEMS on flexible substrates, in collaboration with the Georgia Tech-CNRS IRL and IMS. Due to its unique properties, namely high intrinsic crystal quality, low chemical reactivity, piezoelectric properties, and the presence of a two-dimensional gas at the GaN/AlGaN interface useful for implementing effective transduction means, the use of III-N heterostructures opens the way to a new class of flexible MEMS sensors for applications such as implantable sensors or sensors for extreme conditions. Traditionally, III-N MEMS are manufactured by epitaxial growth on silicon substrates, followed by substrate etching to create suspended structures. The innovative process proposed in this project is based on the Van der Waals selective epitaxy method, which avoids the subsequent etching steps typically used to create MEMS geometries and allows for mechanical detachment and transfer of structured III-N layers onto flexible substrates.
Researchers
Liviu Nicu, Thierry Leïchlé
Engineer
Fabrice Mathieu
Project
ANR AAPG FLEXIGAN (2023-2026) in collaboration with IRL Georgia Tech-CNRS IRL at Metz/Atlanta and IMS at Bordeaux.
Wireless System for Intracranial Pressure Monitoring Based on a 3D-Printed Piezo-Capacitive Sensor
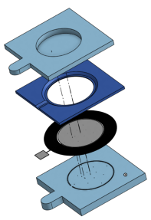
Increased intracranial pressure (ICP) is a critical problem, and its continuous measurement is essential for diagnosis and treatment evaluation. However, current systems rely on catheters penetrating the skull, which introduces significant constraints. This project aims to design an innovative wireless real-time ICP monitoring system. It is based on a 3D-printed piezo-capacitive implantable sensor capable of accurately and continuously measuring intracranial pressure. This implant can also be adapted to measure other types of pressures (e.g., arterial). Funded by the ANR Wisper project, this device proposes a new strategy for wireless implants and opens innovative perspectives for MEMS design through 3D printing.
Site internet du projet Wispers
Researchers
Vincent Mansard, Constandina Arvanitis, Christian Bergaud
Engineer
Pierre-François Calmon
Project
ANR AAPG WISPERS(2023-2027) in collaboration with the MINC team at LAAS-CNRS
Artificial Muscle Using Active Macroporous Gels

There is a growing need for actuators more performant than electric motors, particularly with the rapid development of robotics and the Internet of Things. Among the promising solutions, some rely on active materials capable of controlled deformation.
In our team, we explore the use of flexible smart gels, sensitive to stimuli such as pH or temperature. These gels exhibit very significant deformations, making them particularly suitable for manufacturing bio-inspired artificial muscles. By adding porosity in the range of 10 to 100 µm to these gels, we have shown that this approach allows for a considerable reduction in the response time of smart gels. Thanks to this advancement, we have explored potential applications, including the fabrication of a bio-inspired linear contraction artificial muscle or a digital system for Braille display.
Researcher
Vincent Mansard
Publications
A macroporous smart gel based on a pH-sensitive polyacrylic polymer for the development of large size artificial muscles with linear contraction, Vincent Mansard, Soft Matter, 2021, 17, 9644-9652
Development of a Soft Actuator from Fast Swelling Macroporous PNIPAM Gels for Smart Braille Device Applications in Haptic Technology, R. B. Yilmaz et al., ACS Applied Materials & Interfaces, 2023, 15, 5, 7340–7352
Low-Tech System for Measuring Locomotion Forces in Insects
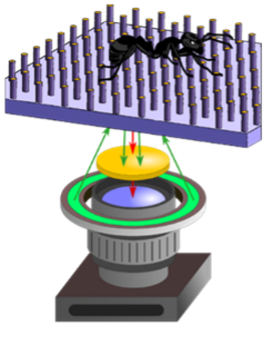
Insects present a fascinating diversity of locomotion strategies that allow them to move efficiently in complex environments. This capability inspires innovations in robotics and materials science. While the kinematics of insect movements (analysis of body segment displacements) has been extensively studied, the dynamics (forces involved in these movements) remains largely unexplored.
In our team, we are developing a system to measure ground reaction forces (GRF), which are essential for understanding how insects accelerate, decelerate, or adapt their locomotion based on different surfaces. Measuring GRF in insects poses a challenge due to the low intensity of the forces involved (ranging from 1 to 100 µN). Our new measurement system, based on PDMS micro-pillars, allows simultaneous measurement of GRF for each leg with a resolution of 1 µN, while covering a large observation area (2 cm). This system, which is low-cost and easily adaptable, provides a robust solution for studying insect locomotion in various environments.
Researchers
Vincent Mansard, Christian Bergaud
Collaboration
Vincent Fourcassié, CRCA, Toulouse